▶新着記事を公式LINEでお知らせしています。友だち申請はこちらから!
▶ICCの動画コンテンツも充実! YouTubeチャンネルの登録はこちらから!
2020年12月某日、ICC一行は、関西へとオフシーズン恒例の2泊3日CRAFTED TOURへ出かけました。今回訪問したのは、CRAFTEDカタパルトを中心に次回登壇いただく企業を中心に6社です。最終回は、前回CRAFTEDカタパルトに登壇した「インターナショナルシューズ」です。ぜひご覧ください!
ICCサミットは「ともに学び、ともに産業を創る。」ための場です。毎回200名以上が登壇し、総勢900名以上が参加する。そして参加者同士が朝から晩まで真剣に議論し、学び合うエクストリーム・カンファレンスです。 次回ICCサミット FUKUOKA 2021は、2021年2月15日〜2月18日 福岡市での開催を予定しております。参加登録は公式ページをご覧ください。
ICC サミット KYOTO 2020のCRAFTEDカタパルトのインターナショナルシューズ上田 誠一郎さんのプレゼンをご覧になった方はいますか? 会場にも展示されていたスニーカー「brightway」に込められたものづくりへの心と技術、親子3代のストーリーを知って、感動した方も多いのではないでしょうか。
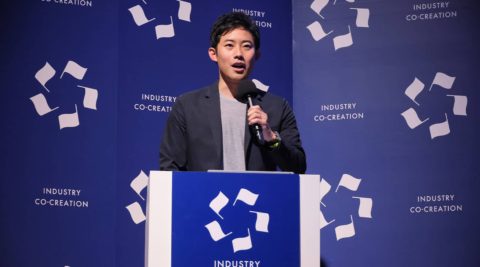
CRAFTEDカタパルトの会場で展示されたbrightway
インターナショナルシューズは、大阪駅から車で約20分、大阪の中心部にあります。社屋はもと輸入車のディーラーだった建物だそうで、外観からは中で靴を作っているようには見えません。
会議室には、「brightway」はもちろんのこと、OEMで作っている靴や、さまざまなブランドの靴が4方の壁にずらりと並んでいます。今回訪問した他社でも目にしましたが、ものづくりの企業は、他社の現物を本当によく研究していらっしゃいます。靴の作りを理解するために、高級婦人靴のクリスチャン・ルブタンであろうと解体するそうです。
靴の作り方を学ぶ〜基本は手作業〜
ICC一行を迎えてくださったのは、1954年創業インターナショナルシューズの3代目、上田 誠一郎さん。老舗の高級婦人靴ブランドの銀座かねまつでの勤務を経て、2015年に家業に戻ってきました。ずっと社名が表に出ない靴のOEM工場でしたが、2020年に初めて自社ブランドシューズである「brightway」を発表し、顧客と直接の接点を持つようになりました。
まずは見学前に、上田さんから靴作りの基礎知識を伺いました。
上田さん「一番最初の『ラスト(靴の型)設計』も含めて、靴作りの工程は9つのプロセスがあります。
中底・本底・ヒールなどの寸法を決める設計。革の裁断、裁断したパーツの縫製。そしてメイン工程である靴底を貼ったり、ヒールを取り付けたりする「底付け」。最後にきれいに磨き仕上げる「仕上げ」。多くの工程を経て1足が完成します。
そしてファクトリエ経由で販売している靴の製造工程の動画を見せていただきましたが、すべての工程にはかなり人の手が入っています。靴作りには、どうしても自動化できない作業が多いのだそうです。
▶「もっといい靴を作ろう」という、揺るぎなきDNA(ファクトリエ)
プラスティック製のラスト(木型)は骨の位置まで調べて作成。革靴の底は何層にもなっている
不勉強ながら、型は革部分を立体的に裁断するために使って、革靴は革を土台に縫い合わせながら作っていくものかと思っていました。見学してみると、裁断したパーツを縫製した状態(アッパー)をラスト(木型)にかぶせて様々なパーツを組み合わせていくことがわかりました。そのためにも土台となるラスト設計(木型設計)は大事で、厚みや高さなどをミリ単位で削って調整するようです。
素材である革について〜お尻の革のほうが上質〜
革製品などで使われる革は、基本的には食肉分をとったあとなのだそうです。革は、タンナーと呼ばれる専門の企業が染めて、工場に持ち込まれます。まずは高級レザーから見せていただきました。
上田さん「これが実際に私たちが扱っている革です。カーフレザーという子牛の革で、これで1匹分、一番高級な革です。これでショートブーツが1足分作れるかどうかというくらいです」
もう1足ぐらい作れそうに見えるのに、意外です。余った部分はなるべく無駄にしないように、小さなパーツに利用して、なるべく捨てないように使っているそうです。
上田さん「さまざまな産地の革があり、どの都市のこの皮は傷が少ないなどあります。食肉のように等級もあります。基本は国産で、一部は北米からの輸入です。北米産は、供給が安定しているので、品質的に安定していると言われます」
お話を伺っていて興味深かったのがスエード素材について。以前は起毛しているような見た目から、冬のブーツなどに使われるものでしたが、最近は夏のサンダルなどでも見かけるようになりました。それには産業的に理由があるといいます。
上田さん「革の表面、ツルツルの面を僕たちは『銀面』といっていて、スムースレザーといいます。スエードは、これをひっくり返した裏側、『床面』をけば立たせたものです。
光っている面がスムースレザーで、その裏側をけば立たせるとスエード。実は表裏一体
最近、夏にスエードのサンダルが出回るようになってきています。流行もありますが、ベジタリアンが増えたり、世界的に肉を食べる量が減っている背景もあります。
世界的な食肉の消費量が減った結果、原皮全体の供給量が少なくなり良質な皮も少なくなります。どのメーカーも良質な皮を手に入れたいのですが、資本力のある大手ブランドが先に手に入れます。
そこで、表面に傷があっても、裏返して起毛すると傷は無くなります。スムースレザーよりスエードの方が傷が無く、裁断の歩留まりも良く生産効率が上がるのです。
メーカーが積極的にスエード素材を使い始めた結果、季節に関係なくスエードのアイテムが並ぶようになりました。
トレンドのように見えて実は世界的な情勢が影響しているという状況があります」
大人の牛の革「ステア」のスエード面。半身分のこのサイズで約12,000〜13,000円
上質の革を自社で供給するために、牧場を買収しているメーカーもあるのだそう。ちなみに食肉でも高級な部位があるように、靴にするにはお尻の部分の革が最適なのだそうです。
上田さん「お尻の部分が一番繊維がつまっていて状態もきれいです。人間と同じで、首にいくほどシワが出ていたりします。だからお尻の革を一番いい場所に使うというルールがあります」
工場見学へ 〜めっちゃ手作り〜
靴と革の基本を学んだあとは、待望の工場見学です!靴作りのプロセスに則って、まずは裁断から見ていきます。
靴作りプロセス①裁断
上田さん「革靴を作るときの特徴として、こちらの両面に刃がついた抜型で革を裁断します。
裁断するときにはクリッカーという機械で裁断します。ボタンを押すと空気圧で機械が動きます。
抜型を反転させることで左右の足のパーツを裁断できます」
靴作りプロセス②縫製の前の準備
上田さん「これはブーツ用の加工なのですが、革に形状記憶のシートを貼ります。ブランドさんの求める履き心地を実現するために薄いものを使ったり、筒を立たせたいときは、もっと分厚いシートを使ったり。素材も使い分けています」
白く見えるのが形状記憶シート。機械では均一にできないため、1枚1枚アイロンをかける
靴作りプロセス③カーブに沿って曲げる
足の部分から足首につながる筒へ、一枚革で作ってあるブーツがありますよね? あのカーブは、どうやって作っているかご存知ですか? 「立体パターン」という加工を、見学させていただきました。
これがその秘密のマシンです。いわば、ホットプレスのサンドイッチを作るような感覚とでもいいましょうか? こちらの機械を使い、熱と力と時間をかけて革を変形させます。
白い鉄板の台の上に、中心の黒い鉄板が中心になるように、1枚の革をセットすると、革が中に吸い込まれて見えなくなりました。中では挟まれた革が、グイーッと伸ばされているそうです。鉄板の温度は90度ぐらいの熱さ、時間は20秒に設定。20秒後に革が上がってきました。
上の形状記憶シートを貼っていた革が、見事にブーツのカーブを描いた形に変形
上田さん「デザインによって角度を変えていて、実はヒールの低いブーツのほうが大変です。たとえばもっと曲げたいというときには、何度もかけたりします。革の伸びを計算して、斜めに入れたり、縦に入れることもあります。時間のかかる工程で、機械が引っ張ったときに傷がついたりすることもあり、そうなると使えなくなります。
ブーツの生産は6〜8月がピークで、その期間はここに入り浸りです。窓の外に淀川が見えるのですが、その時期に花火大会があって毎年ここから見るのが恒例です(笑)」
靴作りプロセス④曲げた革を手作業でカット
曲げた革を型に合わせて、なんとフリーハンドでカットします。
上田さん「曲がった革を1枚1枚カットしています。彼は熟練の職人なので、線に沿ってカットできます。
大量生産のところは、さきほどの抜き型みたいなもので裁断する工場さんも多いです。そちらのほうが圧倒的に効率はいいのですが、どうしても本来のパターン設計と合わなくなってきます。特にロングブーツが難しい。上の部分が2〜3mmずれるだけで、筒がまっすぐ立たなくなります」
ミリ単位を気にするものづくり。これぞCRAFTEDですよね!
靴作りプロセス⑤断面を処理
革を切った断面が白いままでなく、ちゃんと色が塗ってあると高級な感じがしませんか? それもこの流れで行ないます。これで縫製前の準備は終了、と思いきや、まだもう1工程ありました。
靴作りプロセス⑥革漉き
上田さん「履き口の部分などは断面は切りっぱなしになっていなくて、折りたたんでミシンをかけているのですが、例えば分厚い革はそのままだと、折りたたむとごつくなってしまいます。そこで、機械で厚さを削ぐようにスライスしていきます」
左の写真に写っている機械の中央、銀色に見える部分が回転していて、そこに革を一瞬当てると、下にはわずかに鉛筆の削りカスのようなものが落ちていきます。革を見ると、右の写真の黒い革の上部の色が変わっている部分は、革の厚さが薄くなっています。
上田さん「この処理を行うことで、本当にピシッときれいなラインが生まれます。
連結する場所やパーツ同士によって、削る厚さや幅のスライス具合を買えています。これが縫製に入る前の準備段階です」
靴作りプロセス⑥折り込み
上田さん「いまから女性のパンプスの縫製をお見せするのですが、新品のときに、足の甲の部分に履き込み口が当たって痛いときがありますよね。
その理由の一つが、伸び止めや裂け止めのために内側に入っている細いテープです。これに糊を塗って、さきほどの削いだ部分に貼って織り込んでいくのですが、このテープと糊が最初は硬いので、足に当たると痛くなります。
折りたたむときは、カーブのところがそのままだと曲がらないため、包丁で少しずつ切り込みを入れます。brightwayのスニーカーもそういう作り方をしています」
彫刻刀のようなもので丁寧に切り込みを入れて折り返し、金槌で叩いてしっかり癖付けます。
美しく均等に入った切れ込みが見えますね!すごい!これぞCRAFTED。
靴作りプロセス⑦裏地を縫い付ける
上田さん「織り込んだ側に裏地を貼って、皆様の足に当たる部分を縫っていきます」
際にステッチを入れていくのは、本当に職人技! 細かいところを丁寧に縫っていきます。ちなみに靴作りに使うミシンは、立体をあらゆる角度から縫うために、下は平面の台ではなくて一本足のような小さなお立ち台があり、それに乗せて縫っていきます。
上田さん「これもデザインによって、糸の太さやピッチ幅を買えています。きれいなヒールのパンプスなどは、糸もかなり細く、ピッチも細かくかけていきます。
私がかけると波打ってしまうのですが、彼は本当にピシッとかけることができるので、すごい技術だと思います」
縫い終わったら、余分な裏地を切り取って終了。さてさて次の工程は?
上田さん「パンプスの後ろの部分のパーツを連結させたら縫製は完了です。
こうやって作っていく工程で、傷が出てしまって作り直さなければいけないときがあります。そういうときは一部のパーツだけを付け替えることもあるのですが、彼ら職人がすごいのは、1回ミシンで開けた穴と同じ穴に通して縫っていくことができるのです。
ここにいるスタッフは30年以上のキャリアを持つ熟練の方々が多いです。私が入社する前からインターナショナルシューズのものづくりを支えてくださってます」
パンプスの革の部分が縫い終わりました!
ここでbrightwayトリビアを1つ。インターナショナルシューズのDNAがこの写真に写っています!
ジグザグ部分にご注目ください
上田さん「ロングブーツの裏地の部分を重ねて縫うと段差が表面から見えてしまうので、段差が見えないように重ねず、このようにジグザグにステッチをかけます。千鳥ミシンとよばれる縫い方です。
インターナショナルシューズは、ずっとロングブーツを作ってきました。そのルーツをここにさりげなく、アイコンとして入れています」
靴作りプロセス⑧かかとに革の芯材を入れる
靴のかかと部分で硬い箇所がありますよね。そこには芯材が入っています。スニーカーなど履きつぶすと、かかとから固いのが飛び出してきますよね? あれが芯材です。
上田さん「基本的に私たちはほとんどの靴に革の芯材を使っています。一般的なスニーカーや、比較的低価格の靴は、中にプラスチックや樹脂の芯材が入っています。
革の芯材は作業する前日の夜にバケツの水に浸けて、ほどよく濡らして半乾きの状態にしておきます。濡れすぎでも、乾燥していてもだめです。
芯材の素材それぞれに良さはあります。革の芯材の良さは、履いていただくうちに足に馴染んでくること。パンプスなどだと、ずっと履いていると伸びてしまって、スポスポと脱げるようになってしまいますが、例えばドライヤーで温めて、形を戻してあげると新品の時の形に戻ります。
プラスチックだと、もとから固定されているので作るときは作業がしやすいのですが、入れ間違えると段差ができてしまったりします。
革はプラスチックに比べてコストは5倍、自然乾燥の時間もあるので、2〜3倍の時間がかかります。
手間暇かかるのですが、創業者が「履いてくださった方が、長く快適に履けるように」ということで、創業以来、ほとんどの靴にこの革の芯材を使っています」
靴作りプロセス⑨ラスト(木型)に革を被せて中底に固定する
ここからは、brightwayにソールをつけていく過程を見せていただきました。
これが縫製が終了した、brightway。仮のビニール紐が通されています
上田さん「スニーカーのラストに縫製の終わった革を被せて、ソールの中底というボードを取り付けていきます」
まずはつま先部分の革を、マシンを使って固定していきます。1足1足手作業です。この機械、すごくないですか? 両手や足まで使って操作します。
職人さんが足元のペダルを踏み、ハンドルを取り付けて回し、レバーを引くと、ラストに被さっていた革が底にシュッと巻き付いていきました。
上田さん「革の伸びが1枚1枚違うので、ある程度機械と、人がレバーで引っ張って、左右揃うように調整しています。ここで7割調整をして、最後1〜2割は手作業で直していきます。
かかとの部分を叩いているのは、水で濡らした芯材をしっかりかかとにフィットさせるため。ラストにぴったり合うように叩いてなじませています」
続いてはかかとを固定します。中心部に針いっぱいの機械です。
この機械にかかと部分を差し込むと、空気圧により20本の針が一瞬で打ち込まれます。
次から次へと新しい機械に移っていきます。革を巻き込んだ段差をなるべく平らにするように削るマシンとか……
スニーカーのソールをよりしっかり貼り付けるため、ソールの糊を暖めるヒーター、バキュームでより密着させる装置などがあります。
黒いところにセットして蓋を締めるとバキュームで密着度を高める
工程の途中では、何度も想いを込めるように靴を叩いています。
これでbrightwayは完成!なのですが、ラストを外さなければなりません。紐をゆるめると簡単に取れそうですが、すごく力がかかるものなのだそう。以前の方法を見せていただくと、まさに体重をかけて引っこ抜く感じ。今は機械を使って一瞬で外せます。(写真左が以前の手作業・右が現在)
靴作りプロセス<おまけ>ヒールのある靴ならば
ここまで読んでこられた方ならば想像つくかもしれませんが、ヒールの取り付けで、再び拷問器具のような機械が登場します。これは靴の本体にヒールを取り付ける機械で、この穴から釘がドスドス出てきます。
ヒール側から釘を打つパターンと、靴の内側から釘を打つパターンがあります。
インターナショナルシューズは、さまざまな靴ブランドのOEM製造をしていますが、同時に修理のリペアサービスも行っています。ヒール取替や靴のソールの貼替えなどをしたあとに、再びきれいに履いてもらえるように、仕上げ直しを当てて、クリームを塗って、新品のような形にしてお客様にお返ししているそうです。
10年前のブーツも普通に修理依頼が来るそうで、brightwayもそういう靴にしたいと作っているそうですよ。
出来上がった靴は、最後にもう一度傷がないかどうか、左右揃っているか、ファスナーの高さが揃っているかどうかを確認して、箱に入れて出荷されます。ヒール取り付けで釘をたくさん使っているデザインのものは、安全な状態で出せるかどうかX線検査もしています。
見学を終えて
履く人がきれいに、快適に履いてくれるよう想いを込め、職人の技術によって、数多くの工程を経て完成する一足の靴。作っていく細かなプロセスを見学すると、靴の値段は安いのでは?と思ってしまいます。
それに何より、見学後は靴を大切に履こうという気持ちになりました。靴工場といっても、機械で自動的に作っているわけではなく、1足1足、こんなにも人の手がかかっているのです。
今回の見学に先立って、関西在住のICCサミット運営スタッフも見学をさせていただきました。2回に渡ってご案内いただいた上田さん始め、最後に撮影に応じていただいた現社長の上田 陽一さん、インターナショナルシューズの皆様、どうもありがとうございました。以上、現場から浅郷がお送りしました。
(終)
▶新着記事を公式LINEでお知らせしています。友だち申請はこちらから!
▶ICCの動画コンテンツも充実! YouTubeチャンネルの登録はこちらから!
編集チーム:小林 雅/浅郷 浩子/戸田 秀成
更新情報はFacebookページのフォローをお願い致します。